Metal Cutting · Production Engineering · GATE ME
Marks 1
The grinding wheel used to provide the best surface finish is
Marks 2
A cutting tool provides a tool life of 60 minutes while machining with the cutting speed of 60 m/min. When the same tool is used for machining the same material, it provides a tool life of 10 minutes for a cutting speed of 100 m/min. If the cutting speed is changed to 80 m/min for the same tool and work material combination, the tool life computed using Taylor’s tool life model is _______ minutes (rounded off to 2 decimal places).
In an ideal orthogonal cutting experiment (see figure), the cutting speed V is 1 m/s, the rake angle of the tool α = 5°, and the shear angle, 𝜙, is known to be 45°.
Applying the ideal orthogonal cutting model, consider two shear planes PQ and RS close to each other. As they approach the thin shear zone (shown as a thick line in the figure), plane RS gets sheared with respect to PQ (point R1 shears to R2, and S1 shears to S2).
Assuming that the perpendicular distance between PQ and RS is 𝛿 = 25 μm, what is the value of shear strain rate (in s-1 ) that the material undergoes at the shear zone?
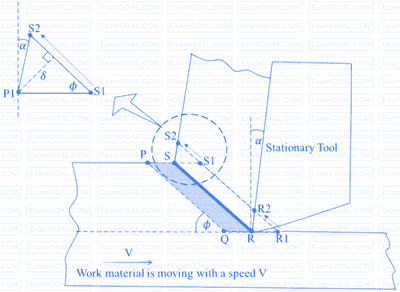
A CNC machine has one of its linear positioning axes as shown in the figure, consisting of a motor rotating a lead screw, which in turn moves a nut horizontally on which a table is mounted. The motor moves in discrete rotational steps of 50 steps per revolution. The pitch of the screw is 5 mm and the total horizontal traverse length of the table is 100 mm. What is the total number of controllable locations at which the table can be positioned on this axis?
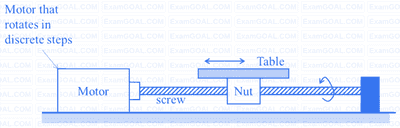
The atomic radius of a hypothetical face-centered cubic (FCC) metal is (√2/10) nm. The atomic weight of the metal is 24.092 g/mol. Taking Avogadro’s number to be 6.023 × 1023 atoms/mol, the density of the metal is ____________ kg/m3 .
(Answer in integer)
A straight-teeth horizontal slab milling cutter is shown in the figure. It has 4 teeth and diameter (D) of 200 mm. The rotational speed of the cutter is 100 rpm and the linear feed given to the workpiece is 1000 mm/minute. The width of the workpiece (w) is 100 mm, and the entire width is milled in a single pass of the cutter. The cutting force/tooth is given by F = Ktcw, where specific cutting force K = 10 N/mm2, w is the width of cut, and tc is the uncut chip thickness.
The depth of cut (d) is D/2, and hence the assumption of $\frac{d}{D}<<1$ is invalid. The maximum cutting force required is ______ KN (round off to one decimal place).
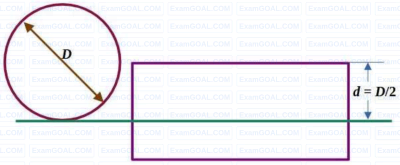
$$\eqalign{ & Tool\,\,1:\,\,\,\,\,\,\,V{T^{0.1}} = 150 \cr & Tool\,\,2:\,\,\,\,\,\,\,V{T^{0.3}} = 300 \cr} $$
where $$V$$ is cutting speed in $$m/minute$$ and $$T$$ is tool life in minutes. The breakeven cutting speed beyond which Tool $$2$$ will have a higher tool life is _______________ $$m/minute$$.
$$P.$$ reduction in friction angle increases cutting force
$$Q.$$ Reduction in friction angle decreases cutting force
$$R.$$ Reduction in friction angle increases chip thickness
$$S.$$ Reduction in friction angle decreases chip thickness
$$\eqalign{ & \,\,\,\,\,\,\,\,\,\,\,\,Carbi{\mathop{\rm de}\nolimits} \,\,tool:\,\,\,\,\,\,\,\,\,\,\,\,V{T^{1.6}} = 3000 \cr & \,\,\,\,\,\,\,\,\,\,\,\,HSS\,\,tool:\,\,\,\,\,\,\,\,\,\,\,\,\,\,\,\,\,\,\,\,\,V{T^{0.6}} = 200 \cr} $$
Where $$V$$ is the cutting speed in $$m/min$$ and $$T$$ is the tool life in $$min.$$ The carbide tool will provide higher tool life if the cutting speed in $$m/min$$ exceeds
The normal force acting at the chip-tool interface in $$N$$ is
The orthogonal rake angle of the cutting tool in degrees is
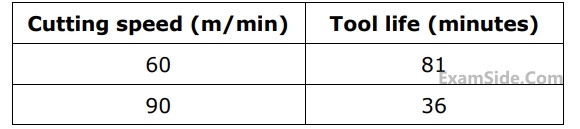
What is percentage increase in tool life when the cutting speed is halved.
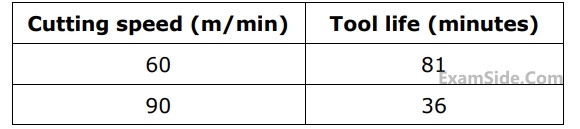
The exponent $$(n)$$ and constant $$(K)$$ of the Taylor's tool life equation are
The cutting and frictional forces respectively are
The shear plane angle (in degrees) and the shear force respectively are
Neglect over travel or approach of the tool. When tool life is $$20min,$$ the machining time in $$min$$ for a single pass is
When tool life is $$20min.$$ The cutting velocity in $$m/min$$ is
$$\,\,\,\,\,\,\,\,\,\,$$Uncut thickness $$\,\,\,\,\,$$ $$= 0.5$$ $$mm$$
$$\,\,\,\,\,\,\,\,\,\,$$Cutting speed $$\,\,\,\,\,\,\,\,\,\,$$ $$= 20$$ $$m/min$$
$$\,\,\,\,\,\,\,\,\,\,$$Width of cut $$\,\,\,\,\,\,\,\,\,\,\,\,\,\,$$ $$= 5$$ $$mm$$
$$\,\,\,\,\,\,\,\,\,\,$$Chip thickness $$\,\,\,\,\,\,\,\,$$ $$= 0.7$$ $$mm$$
$$\,\,\,\,\,\,\,\,\,\,$$Thrust force$$\,\,\,\,\,\,\,\,\,\,\,\,\,\,\,$$ $$= 200$$ $$N$$
$$\,\,\,\,\,\,\,\,\,\,$$Cutting force $$\,\,\,\,\,\,\,\,\,\,\,\,$$ $$= 1200$$ $$N$$
$$\,\,\,\,\,\,\,\,\,\,$$Rake angle $$\,\,\,\,\,\,\,\,\,\,\,\,\,\,\,\,\,$$ $$ = {15^ \circ }$$
Assume Merchant’s theory
The percentage of total energy dissipated due to friction at the tool chip interface is
$$\,\,\,\,\,\,\,\,\,\,$$Uncut thickness $$\,\,\,\,\,$$ $$= 0.5$$ $$mm$$
$$\,\,\,\,\,\,\,\,\,\,$$Cutting speed $$\,\,\,\,\,\,\,\,\,\,$$ $$= 20$$ $$m/min$$
$$\,\,\,\,\,\,\,\,\,\,$$Width of cut $$\,\,\,\,\,\,\,\,\,\,\,\,\,\,$$ $$= 5$$ $$mm$$
$$\,\,\,\,\,\,\,\,\,\,$$Chip thickness $$\,\,\,\,\,\,\,\,$$ $$= 0.7$$ $$mm$$
$$\,\,\,\,\,\,\,\,\,\,$$Thrust force$$\,\,\,\,\,\,\,\,\,\,\,\,\,\,\,$$ $$= 200$$ $$N$$
$$\,\,\,\,\,\,\,\,\,\,$$Cutting force $$\,\,\,\,\,\,\,\,\,\,\,\,$$ $$= 1200$$ $$N$$
$$\,\,\,\,\,\,\,\,\,\,$$Rake angle $$\,\,\,\,\,\,\,\,\,\,\,\,\,\,\,\,\,$$ $$ = {15^ \circ }$$
Assume Merchant’s theory
The values of shear angle and shear strain, respectively are
$$\,\,\,\,\,\,\,\,\,\,$$Uncut thickness $$\,\,\,\,\,$$ $$= 0.5$$ $$mm$$
$$\,\,\,\,\,\,\,\,\,\,$$Cutting speed $$\,\,\,\,\,\,\,\,\,\,$$ $$= 20$$ $$m/min$$
$$\,\,\,\,\,\,\,\,\,\,$$Width of cut $$\,\,\,\,\,\,\,\,\,\,\,\,\,\,$$ $$= 5$$ $$mm$$
$$\,\,\,\,\,\,\,\,\,\,$$Chip thickness $$\,\,\,\,\,\,\,\,$$ $$= 0.7$$ $$mm$$
$$\,\,\,\,\,\,\,\,\,\,$$Thrust force$$\,\,\,\,\,\,\,\,\,\,\,\,\,\,\,$$ $$= 200$$ $$N$$
$$\,\,\,\,\,\,\,\,\,\,$$Cutting force $$\,\,\,\,\,\,\,\,\,\,\,\,$$ $$= 1200$$ $$N$$
$$\,\,\,\,\,\,\,\,\,\,$$Rake angle $$\,\,\,\,\,\,\,\,\,\,\,\,\,\,\,\,\,$$ $$ = {15^ \circ }$$
Assume Merchant’s theory
The coefficient of friction at the tool chip interface is
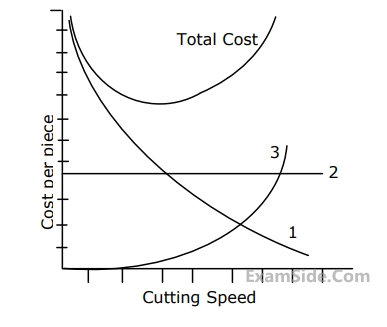
The three curves $$1,2$$ and $$3$$ respectively represent
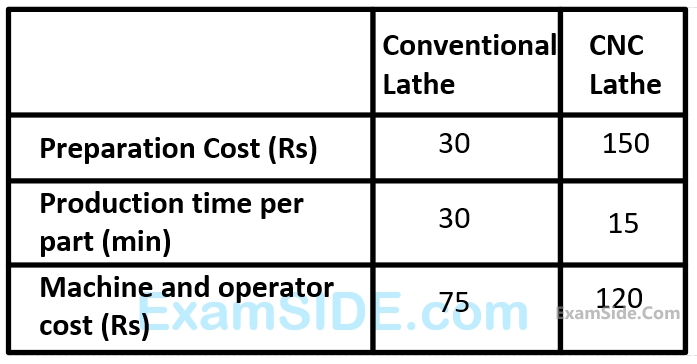
The machine preferred for producing $$100$$ pieces is
(Hint: flank wear rate is proportional to $$\cot \,\alpha $$)
Marks 5
Cutting speed: $$40$$ $$m/min,$$
Depth of cut: $$0.3$$ $$mm,$$
Tool rake angle : $$ + {5^ \circ },$$
Chip thickness: $$1.5$$ $$mm,$$
Cutting force: $$900$$ $$N,$$
Thrust force: $$450$$ $$N$$
Using Merchant's analysis, the Friction angle during the machining will be
The breakeven production batch size above which the automatic machine tool will be economical to use, will be
In the above problem, the coefficient of friction at the chip tool interface obtained using Earnest and Merchant theory is
The thickness of the produced chip is
Rake angle $$=35deg,$$
Feed rate $$=0.1mm/rev$$
Cutting force $$=2000N,$$
Cutting speed $$=15m/min$$
Length of continuous chip is one revolution $$=60mm$$
Feed force $$=800N.$$ Calculate the chip thickness, shear plane angle, velocity of chip along tool face and coefficient of friction.
Also calculate the corresponding tool life. If you have to machine at a cutting speed of $$1m/s$$, then which one of these tools will you choose in order to have less frequent tool changes?
The values of normal rake and normal clearance of the above mentioned tool .............
Work material : steel,
Tool material : $$HSS,$$
Depth of cut : $$1.6mm,$$
Feed : $$0.8mm/rev$$
Cutting speed $$=5.5m/min$$ and power consumed $$=0.67$$ $$kW$$
Outside diameter of the tube : $$100mm,$$
Inside diameter of the tube $$=96$$ $$mm$$
$$RPM$$ of the work piece $$=120,$$
Longitudinal feed $$=0.5mm/rev$$
Cutting ratio $$=0.3,$$
Tangential force $$=800N,$$
Axial force $$=600N$$
Calculate the chip velocity in $$m/min$$ and the total power consumption in $$KW$$
Uncut chip thickness $$=0.25mm,$$ Cutting speed: $$60m/min,$$ Tool rake angle: $$0$$ Chip thickness $$0.75mm,$$ Cutting force : $$900$$ $$N$$, Thrust force : $$450$$ $$N$$
Calculate the shear angle, total power in making the cut and coefficient of friction between the chip tool interface.
$$\eqalign{ & HSS\,\,tool\,:\,\,\,\,\,\,\,\,\,\,\,\,\,\,\,V{T^{0.1}} = 200 \cr & Carbide\,\,tool\,:\,\,\,\,\,\,\,V{T^{0.35}} = 500 \cr} $$
Find out the break even speed above which the carbide tool will be economical.