Metal Cutting · Machine Tools and Machining · GATE PI
Marks 1
(a) increase / reduction
(b) increase / decrease
(a) increasing / reducing
(b) increasing / reducing
(a) decreases/ increases
(b) spoils / improves
Marks 2
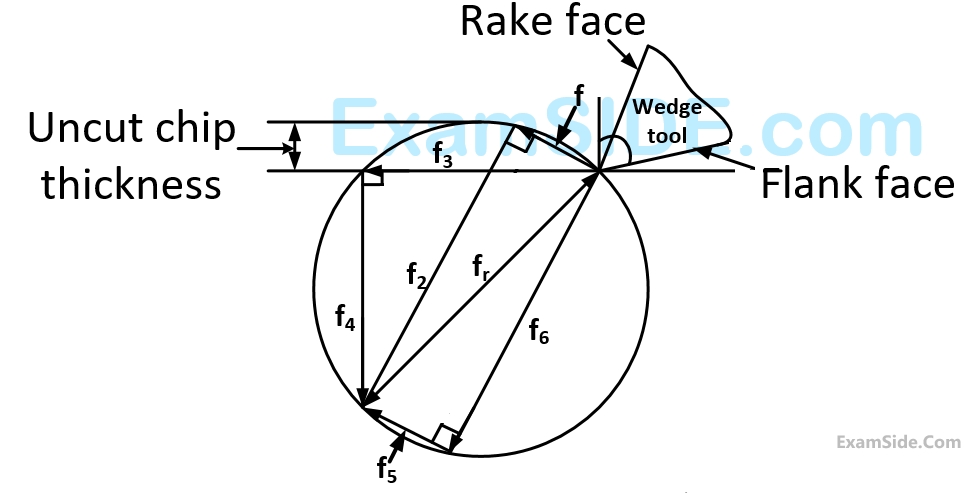
The coefficient of friction can be estimated from the ratio
where, $$C$$ is a constant. The suggested values for the cutting parameters are: $$V=1.5$$ $$m/s,$$ $$f=0.25$$ $$mm$$ and $$d=3$$ $$mm$$ for normal rough turning. If the operation is performed at twice the cutting speed and the other parameters remain unchanged, the corresponding percentage change in tool life is ______________.
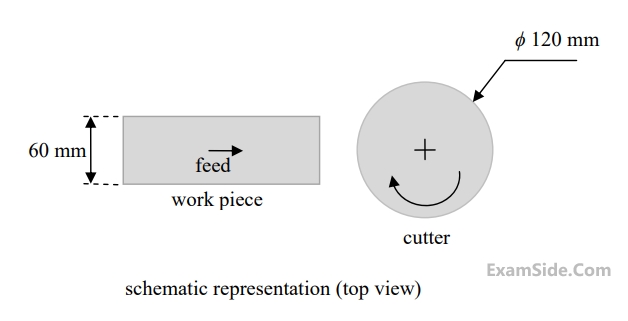
The orthogonal rake angle of the cutting tool in degree is
The normal force acting at the chip-tool interface in $$N$$ is
$$\eqalign{ & \,\,\,\,\,\,\,\,\,\,\,\,Carbi{\mathop{\rm de}\nolimits} \,\,tool:\,\,\,\,\,\,\,\,\,\,\,\,V{T^{1.6}} = 3000 \cr & \,\,\,\,\,\,\,\,\,\,\,\,HSS\,\,tool:\,\,\,\,\,\,\,\,\,\,\,\,\,\,\,\,\,\,\,\,\,V{T^{0.6}} = 200 \cr} $$
Where $$V$$ is the cutting speed in $$m/min$$ and $$T$$ is the tool life in $$min.$$ The carbide tool will provide higher tool life if the cutting speed in $$m/min$$ exceeds
Chip thickness ratio $$0.4$$
Under formed thickness $$0.6mm$$
Rake angle $$ + {10^0}$$
Cutting speed $$2.5m/s$$
Mean thickness of primary shear zone $$25microns$$
The shear strain rate in $${s^{ - 1}}$$ during the process is
Automat will be economical if the batch size exceeds
The shear angle (in degrees) is
The chip velocity (in $$m/min$$) is
Given : Width of cut $$=3.6mm;$$
Shear strength of work piece material $$460N/m{m^2};$$
Depth of cut $$=0.25mm;$$
Coefficient of friction at chip tool interface $$=0.7.$$
Minimum Power requirement (in $$KW$$) at a cutting speed of $$150m/min$$ is
Given : Width of cut $$=3.6mm;$$
Shear strength of work piece material $$460N/m{m^2};$$
Depth of cut $$=0.25mm;$$
Coefficient of friction at chip tool interface $$=0.7.$$
Shear plane angle (in degrees) for minimum cutting force is
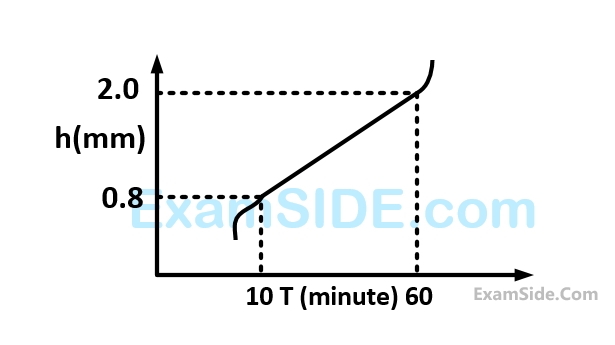
For a critical wear land of $$1.8mm,$$ the cutting tool life (in $$min$$) is
Cutting force $$=1200N ;$$ Thrust force $$=500N$$
Tool rake angle $$=zero ;$$ Cutting speed $$=1$$ $$m/s,$$
Depth of cut $$=0.8mm;$$
Chip thickness $$=1.5$$ $$mm$$
Chip speed along the tool rake face will be
Cutting force $$=1200N ;$$ Thrust force $$=500N$$
Tool rake angle $$=zero ;$$ Cutting speed $$=1$$ $$m/s,$$
Depth of cut $$=0.8mm;$$
Chip thickness $$=1.5$$ $$mm$$
Friction angle during machining will be
$$\,\,\,\,\,\,\,\,\,\,\,$$Back rake angle $$=15deg,$$
$$\,\,\,\,\,\,\,\,\,\,\,$$Width of cut $$=2mm,$$
$$\,\,\,\,\,\,\,\,\,\,\,$$Chip thickness $$=0.4mm,$$
$$\,\,\,\,\,\,\,\,\,\,\,$$Feed rate $$=0.2mm/rev.$$
The shear angle is
$$1.$$ $$\,\,\,\,\,\,\,\,\,\,\,\,$$ As the cutting speed increases, the cost of production initially reduces, then
$$\,\,\,\,\,\,\,\,\,\,\,\,$$after an optimum cutting speed it increases.
$$2.$$ $$\,\,\,\,\,\,\,\,\,\,\,\,$$ As the cutting speed increases the cost of production also increases and
$$\,\,\,\,\,\,\,\,\,\,\,\,$$after a critical value to it reduces.
$$3.$$ $$\,\,\,\,\,\,\,\,\,\,\,\,$$ Higher feed rate for the same cutting speed reduces cost of production.
$$4.$$ $$\,\,\,\,\,\,\,\,\,\,\,\,$$ Higher feed rate for the same cutting speed increases the cost of production
Which of the statements given above are correct?
The number of components per tool life
Applying Taylor's equation $$V{T^{0.25}} = 160,$$ the tool life in minutes is
If the friction angle at the tool-chip interface is $${58^ \circ }$$ $$10'$$ and the cutting force components measured by a dynamometer are $$600$$ $$N$$ and $$200$$ $$N$$, the power loss due to friction (in $$kNm/min$$) is approximately
The velocity (in $$m/min$$) with which the chip flows on the tool face is
$$\,\,\,\,\,\,\,\,\,\,\,$$Back rake angle $$=15deg,$$
$$\,\,\,\,\,\,\,\,\,\,\,$$Width of cut $$=2mm,$$
$$\,\,\,\,\,\,\,\,\,\,\,$$Chip thickness $$=0.4mm,$$
$$\,\,\,\,\,\,\,\,\,\,\,$$Feed rate $$=0.2mm/rev.$$
If the cutting force and the thrust force are $$900N$$ and $$810N,$$ the mean strength in $$Mpa$$
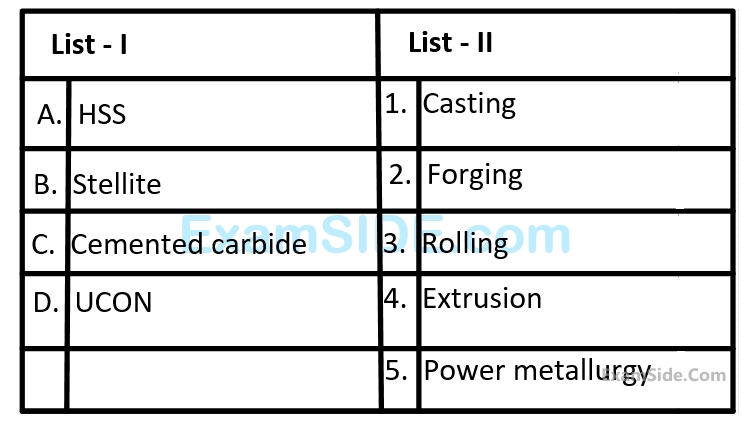
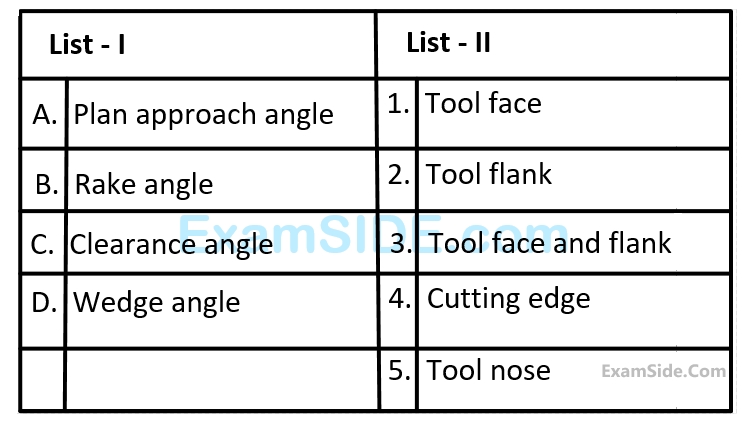
During the third stage of tool-wear, rapid deterioration of tool edge takes place because
$$1.$$ Flank wear is only marginal.
$$2.$$ Flank wear is large.
$$3.$$ Temperature of the tool increases gradually.
$$4.$$ Temperature of the tool increases drastically.
Which of the statements given above are correct?
$$1.$$ This affects the direction of chip flow.
$$2.$$ This reduces excessive friction between the tool and work piece
$$3.$$ This affects tool life
$$4.$$ This allows better access of coolant to the tool-work piece interface
Which of the statements given above are correct?
$$\eqalign{
& HSS:\,\,\,\,\,\,\,\,\,\,\,\,\,V{T^{0.2}} = 150 \cr
& Carbide:\,\,\,\,\,\,V{T^{0.3}} = 250 \cr} $$
Where $$V$$ is the cutting speed in $$m/min$$ and $$T$$ is the tool life in $$min.$$ The breakdown cutting speed above which the carbide tool will be beneficial is
Marks 5
The coefficient of friction between the chip and tool will be
The shear force in cutting will be
The following data were given
$${S_0} = $$ feed $$=0.12$$ $$mm/rev$$
$$T=$$ depth of cut $$=2.0$$ $$mm$$
$${a_2} = $$ chip thickness $$=0.22$$ $$mm$$
$${V_f} = $$ chip velocity $$=52.6$$ $$m/min$$
$${\tau _s} = $$ dynamic yield shear strength $$=400$$ $$MPa$$
$${P_z} = $$ main cutting force $$ = {S_0}\,t\,{\tau _s}\left( {\zeta \,\sec y - \tan \gamma + 1} \right)$$
Where $$\zeta = $$ chip reduction coefficient and $$\gamma = $$ orthogonal rake.
The main cutting force $$\left( {{P_z}} \right)$$ and cutting power assuming orthogonal machining are
$$i)$$ For the given conditions, the tailor's exponent and constant are .............
$$ii)$$ The optimum cutting speed, $${V_{opt}},$$ neglecting the work-piece and tool changing times is
The coefficient of friction between the chip tool interfaces will be
Chip velocity is
Area of shear plane is
The depth of cut $$=2$$ $$mm,$$
Width of cut $$=15$$ $$mm,$$
Cutting speed $$=0.5$$ $$m/s$$ and
The rake angle $$=0$$ deg.
The cutting force and the thrust force are respectively $$900$$ $$N$$ and $$600$$ $$N$$ and the shear angle $$=30$$ $$deg$$.
The cutting power in watts is
The depth of cut $$=2$$ $$mm,$$
Width of cut $$=15$$ $$mm,$$
Cutting speed $$=0.5$$ $$m/s$$ and
The rake angle $$=0$$ deg.
The cutting force and the thrust force are respectively $$900$$ $$N$$ and $$600$$ $$N$$ and the shear angle $$=30$$ $$deg$$.
The average coefficient of friction between the chip and the tool is
Shear velocity with the help of a velocity triangle.
The shear angle is
The tangential force on the tool is
The maximum power requirement for the operation is
The depth of cut $$=2$$ $$mm,$$
Width of cut $$=15$$ $$mm,$$
Cutting speed $$=0.5$$ $$m/s$$ and
The rake angle $$=0$$ deg.
The cutting force and the thrust force are respectively $$900$$ $$N$$ and $$600$$ $$N$$ and the shear angle $$=30$$ $$deg$$.
The length of the shear plane is
$$\,\,\,\,\,\,\,\,\,\,$$$$\,\,\,\,$$ $$V{T^a}{F^b}{D^c} = K,$$
Where $$V=$$ Cutting speed, meters/min,
$$\,\,\,\,\,\,\,\,\,\,\,\,\,\,\,$$ $$T=$$ Tool life,
$$\,\,\,\,\,\,\,\,\,\,\,\,\,\,\,$$ $$F=$$ feed, $$mm/rev,$$
$$D=$$ depth of cut in $$mm,$$ Indicates have magnitude $$a=0.3, b=0.3, c=0.15,$$
If the feed is halved and depth of cut doubled, for identical tool life of $$60$$ minutes, the percentage change in speed
$$\,\,\,\,\,\,\,\,\,\,$$$$\,\,\,\,$$ $$V{T^a}{F^b}{D^c} = K,$$
Where $$V=$$ Cutting speed, meters/min,
$$\,\,\,\,\,\,\,\,\,\,\,\,\,\,\,$$ $$T=$$ Tool life,
$$\,\,\,\,\,\,\,\,\,\,\,\,\,\,\,$$ $$F=$$ feed, $$mm/rev,$$
$$D=$$ depth of cut in $$mm,$$ Indicates have magnitude $$a=0.3, b=0.3, c=0.15,$$
The change in productivity for the new processing conditions
The effective rake and clearance angle are
The diameter of the job at which, while parting, the tool will start rubbing
The setup cost and the cost for special tooling on the turret lathe would be $$Rs.3000/-.$$ These costs are negligible on the general purpose lathe. Calculate the batch seize which justifies the use of turret lathe.
Diameter of the finished hole $$=75mm,$$
rise per tooth $$=0.03mm$$
Tooth pitch $$=10mm,$$
Length of the broach $$=750mm$$
Cutting speed $$=6m/min,$$
specific cutting pressure $$ = 1300 \times {t^{0.4}}\,\,N/m{m^2},$$ (Where $$t$$ is the uncut chip thickness)
If the tool and work handling time is $$0.5min,$$ estimate the production rate per hour
If the tool regrinding and changing time is $$15min,$$ the cutting speed for tool $$A$$ $$ahs$$ to be chosen ($$40m/min$$ or $$50m/min$$)